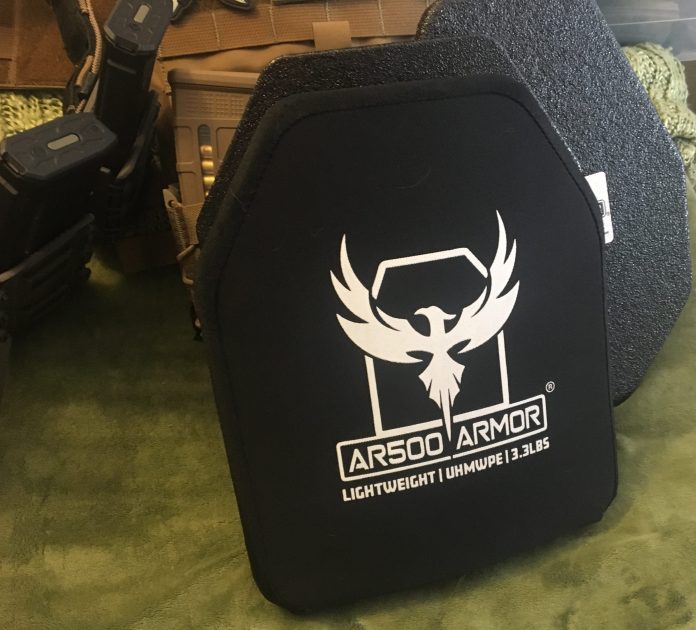
There is a universal truth to armor.
It sucks to wear.
The materials capable of stopping a bullet or shrapnel impact and imposing it between you and that potentially lethal puncture/energy transfer usually carry the characteristic: HEAVY.
The affordable steel plates that AR500 Armor is known for weigh 8lbs each. Combine that with necessary trauma padding or soft armor and a carrier you quickly push 25lbs in a hurry. The level IV selection of composite ceramics provide better protection but no savings in weight.
The stereotypical response to a complaint about armor is “It’s supposed to be comforting, not comfortable.” In short, the burden of armor is a necessary discomfort for the protection. A balancing act of mobility against the ability to stop an impacting gunshot. It ironically makes you a little slower and easier to hit, especially on an unconditioned body. Physical education and conditioning make armor bare-able.
However, thanks to science, we continue to develop and apply materials that do things better.
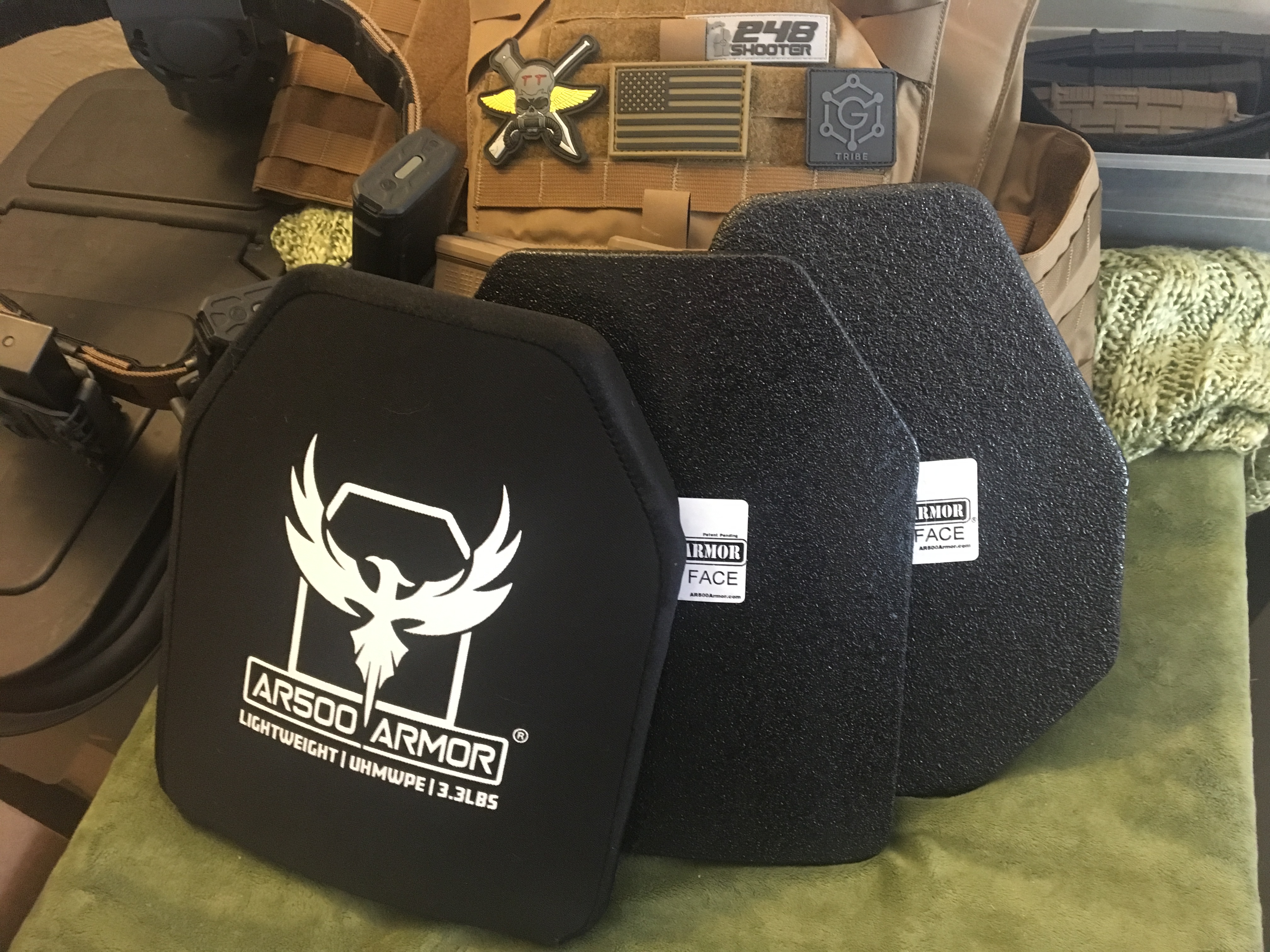
Ultra High Molecular Weight Polyethylene (UHMWPE) offers us several material advantages.
Polyethylene? Yes.
Plastic? Yes.
Ultra-high-molecular-weight polyethylene (UHMWPE, UHMW) is a subset of the thermoplastic polyethylene. Also known as high-modulus polyethylene, (HMPE), it has extremely long chains, with a molecular mass usually between 3.5 and 7.5 million amu.[1]
The longer chain serves to transfer load more effectively to the polymer backbone by strengthening intermolecular interactions. This results in a very tough material, with the highest impact strength of any thermoplastic presently made. –Wikipedia
UHMWPE is odorless, tasteless, and nontoxic.[3] It embodies all the characteristics of high-density polyethylene (HDPE) with the added traits of being resistant to concentrated acids and alkalies, as well as numerous organic solvents.[4] It is highly resistant to corrosive chemicals except oxidising acids; has extremely low moisture absorption and a very low coefficient of friction; is self-lubricating (see boundary lubrication); and is highly resistant to abrasion, in some forms being 15 times more resistant to abrasion than carbon steel. Its coefficient of friction is significantly lower than that of nylon and acetal and is comparable to that of polytetrafluoroethylene (PTFE, Teflon), but UHMWPE has better abrasion resistance than PTFE.
UHMWPE is 8-15 times stronger than steel in strength to weight. It also has a very high chemical neutrality resisting water, oils, and solvents. It’s molecular strength is extremely high but actual density low, making it buoyant.
The polyethylene is made into long molecular aligned fibers and woven into a sheet. When layered with other sheets it allows for exceptional energy transfer reduction between the molecules and layers. The sheets are oriented in varying directions further increasing the overall property strengths of the UHMWPE as the aligned fibers crisscross.
The layers and dissonant orientation of the specialized polyethylene form an energy absorbing ‘catcher’s mitt’ plate that successfully stops rifle rounds. NIJ Level III rated stopping 7.62x51mm (.308), 7.62x39mm, and 5.56x45mm (.223 Rem) multiple hits stand alone (does not need to have a soft armor or carrier component to function). UHMWPE would be a worthy armor candidate on fewer property merits but when the material is formed into 10×12 armor plates they weigh less than half their conventional level III and level IV counterparts.
3.3lbs each and buoyant (won’t sink in water) cuts the overall weight of a kitted carrier down by around 50% while still maintaining level III protection.
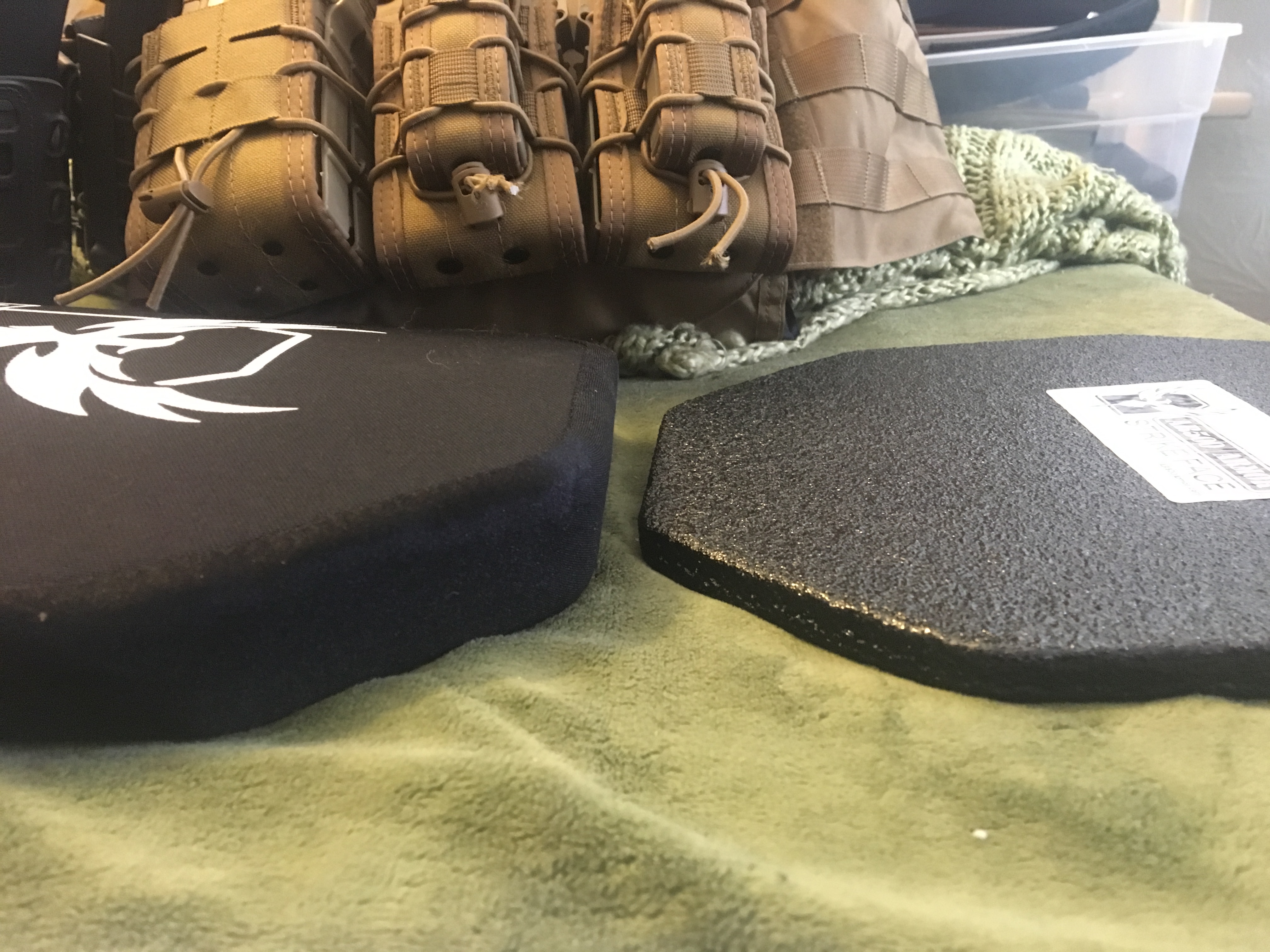
Physically the plates are higher volume but most carriers like my Valkyrie have enough room to accommodate them without issue.
The thick light weight plates are also significantly less fragile than level IV ceramic.
Ceramic body armor plates are fragile, to a degree, being designed to catch a high velocity projectile from the front (or back) strike face. The layered ceramic is designed to crush and break, catching impacting rounds. Once it is broken the plate needs replacement. Ceramic is still a glass product and if dropped, sat on, or torqued in a way that cracks the layers they are now compromised.
The polyethylene (plastic) plates aren’t as vulnerable to unintentional damage from rough handling.
If considering any maritime application the buoyant water proof plates will not sink a water bound wearer or be compromised by immersion. The coast guard, any harbor or coastal deputies, and in any other emergency or duty armored application near water UHMWPE benefits the wearer if they end up in the water.
Putting UHMWPE Polyethylene plates into your armor set up increases comfort, durability, mobility, and water safety (where relevant), while significantly decreasing physical duress and kit weight. Unless you’re requiring a level IV threat protection the PE plates have substantial advantages in a carrier.
It’s an armor material selection or upgrade worth serious consideration, currently my standard plates. They suck much less to wear, almost comfortable.
“No one sweats into their armor or has to go into the rain or water while wearing it and no one uses oils and solvents around firearms while wearing armor. It certainly isn’t heavy and doesn’t cause discomfort so I’m not sure why any of this is advantageous.” – Marine Veteran, after going for a swim with a rifle while in body armor now cleaning said rifle as the heavy SAPI’s and carrier chafe