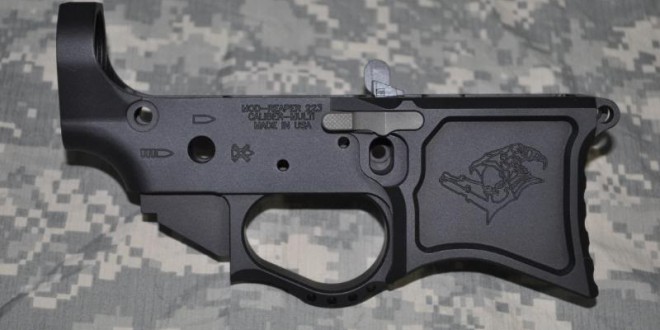
The holiday season is almost upon us or is upon us not sure which. For many of us this is the time of year that we either splurge on a new gun, an upgrade or take on that long put off project of building a weapon.
For those of us newer to building guns starting that project by narrowing down what parts are going into it is the hardest part. Over the next few weeks we will go into the various parts of the AR-15 platform and where to best spend on upgrades and what you can save some money on. If you recall we already did a great article on barrel length.
Today we are going to look at the materials for AR-15 lowers. There is generally 2 grades of aluminum and 2 types of production that will affect the look and cost of a lower.
Aluminum 7075-T6 vs 6061-T6
Early lowers or budget lowers can be built using a 6061-T6 aluminum that is less expensive and less durable. The fact is it is still far stronger then any polymer lower that many people do in fact use without issue. They will hold up just fine for the average plinker or safe queen. That said it is not enough cheaper that I personally would risk my life on it.
7075-T6 is the new “standard” for aluminum used in weapons like the AR-15. It is stronger then its predecessor the 6061-T6 and just as easy to work with.
Here is a comparison chart on the differences:
Alloy and Temper |
Form | Thickness | Material Properties* (KSI unless noted) | ||||||||
Ultimate Tensile Strength Ftu |
Yield Tensile Strength Fty |
Yield Comp. Strength Fcy |
Ultimate Shear Strength Fsu |
Ultimate Bearing Strength Fbru e/D=1.5 |
Yield Bearing Strength Fbry e/D=1.5 |
Modulus of Elasticity E x103 |
|||||
7075-T6 | Billet | 1.001 – 2.000 | 77 | 66 | 64 | 46 | 100 | 86 | 10.3 | ||
7075-T6 | Die Forging | 1.001 – 2.000 | 74 | 63 | 66 | 43 | 104 | 82 | 10.0 | ||
6061-T6 | Billet | 1.001 – 6.500 | 38 | 35 | 34 | 19 | 52 | 42 | 9.9 | ||
6061-T6 | Die Forging | ≤ 4.000 | 38 | 35 | 36 | 25 | 61 | 54 | 9.9 | ||
* – Data taken from DOT/FAR/AR-MMPDS-01 Metallic Materials Properties Development & Standardization, 31 January 2003 |
What is the Machined or Billet?
Machined lower receivers are cut form a solid block of aluminum 7075-T6. The block of raw aluminum if often refereed to as billet. Think of the billet as a block of wood that through chisels or knives you would whittle into a shape. Instead of chisels CNC machines are used to precession cut the block to match a 3d computer model.
How is Forged Different?
Forged lowers take a billet block of aluminum and heat the aluminum to 1/3rd of its melting point making it soft. A mold is then used to press the heated billet into a specific form. This is done using a very heavy several tons of pressure press that can stamp out forged items very fast. There is usually a bit of metal that seeps between the halves of the mold that needs to be trimmed off or smoothed out.
Which is Stronger?
Forged is generally thought to be stronger as you can see in the chart above. The reason for this is when metal cools it forms grains that do not stick together well. The forging process presses those grains together tighter creating a stronger bond and also pushes those grains into a specific pattern that can be used to strengthen the points that receive the most pressure.
The real truth of it is though is evident in the diagram above. There is very little difference in any of the strength values between the forged and the machined parts. The real difference in strength is related to the type of alloy and the form of temper. So if your concern is durability any lower in 7075-T6 aluminum is likely to meet your needs.
Why Does Machined Cost More?
Billet lowers are usually substantially more money then forged lowers. The reason for this is in the manufacturing process, not the strength or quality of the end product.
Remember a machined lower starts with an entire billet block larger than the end product. The block is then reduced down by shaving and cutting the block to the desired specs. The left over aluminum is more or less wasted. Yes it is sold as scrap but when compared to the amount of aluminum used in the forging process you are wasting a lot of metal.
Second the machining process takes a very expensive CNC machine that needs to move the parts around and cut away the parts. The moving of the block and cutting process takes much more time then the simple forged stamping process. Further the cutting blades are expensive and must be kept cool or they will melt.
With forging once the expensive machine is purchased and an initial model is made the cost of operation is very low and the production rate is incredibly high. Forging is like a factory where CNC is like a custom shop. You always pay more for custom since time and materials is money.
Why Does Anyone Buy Machined?
Forging is stronger and cheaper so you are probably wondering why are so many companies selling billet lowers and why would I buy one? Looks are the largest reason. Forged lowers can not have hard 90 degree angles without additional machining, they also tend to have a more rounded look with less straight lines. They tend to be far less adorned then Machined work due to the mass produced nature of the product.
Forged parts require a new mold when changing your product line or adding new features like a different trigger guard or magazine well . This results in shutting down the line to re-tool as well. With CNC machining it is just a matter of running a different program. This makes CNC manufacturing very adaptable to market demand and a wider range of marketable products.
So Which One do I Want?
Honestly I do not know. Don’t you hate that answer when you read a blog. The fact is I can’t answer that for you. All I can do is give you the facts to make a better decision. The answer comes down to what are you using it for, how much do you want to spend, and how important are looks?
My recommendation is go 7075-T6 aluminum. If your budget conscious or really going to beat the hell out of your gun go forged. If you have the money and want the look of some awesome great lines then spend the cash on the billet lower designed the way you want.
I really like the looks of some of the high end Billet lowers that companies like Spikes Tactical and Seekins make. Here are some examples